Understanding the Working Method of Magnetic Powder Cores and Their particular Applications
Magnetic powder snow cores are essential parts in modern electric power electronics, offering productivity, stability, and versatility. With their spread air gaps and advanced material properties, these cores enjoy a critical position in applications this kind of as SMPS (Switched Mode Power Supplies), inductors, and transformer repair. This article explores their working theory, unique features, as well as the various materials which will make them indispensable throughout power management systems.
Working Principle regarding Magnetic Powder Callosité
Distributed Air Gaps:
Magnetic powder cores feature assigned atmosphere gaps distributed through the core. This design enhances energy memory space, reduces core saturation, minimizes stray permanent magnet fields and difference loss errors, and even improves overall performance in DC and even AC conditions.
Inductance Stability:
The distributed air gap ensures consistent inductance throughout various operating circumstances, making magnetic powdered cores ideal with regard to applications requiring precise control.
Thermal in addition to Loss Characteristics:
Substantial resistivity reduces eddy current losses.
Low hysteresis minimizes temperature generation.
Most permanent magnet powder cores avoid thermal aging, guaranteeing durability and dependability.
Core Materials and Their Software
Magnet powder cores are available in various materials, each with specific properties tailored to different power administration needs. Below usually are the most widely used materials:
1. MPP (Molypermalloy Powder Cores)
Key Features:
Lowest core losses among all materials.
High heat stability and AC/DC performance.
Applications:
Flyback transformers, buck-boost transformers, and energy storage space inductors.
Advantages:
Removes stray magnetic fields with its hidden air gap design and style.
2. High Flux Cores
Key Capabilities:
High flux denseness with low recurring magnetism.
Ideal with regard to DC bias-dominated styles.
Applications:
Energy storage inductors for SMPS.
Advantages:
Smaller main sizes handle high currents, which is why they are concidered most affordable.
3. XFLUX Induration
Key Features:
Higher saturation levels and superior performance beneath heavy loads.
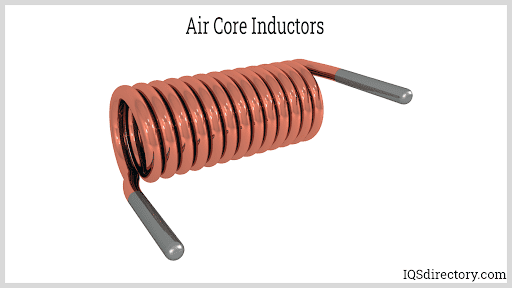
Apps:
Power factor static correction (PFC) circuits, UPS systems, and increase chokes.
Advantages:
Suited for moderate in order to heavy inductor apps.
4. Kool Mu Cores
Key Features:
Low core failures and exceptional energy properties.
Cost-effective when compared with powdered iron cores.
Applications:
Pulse transformer repair, flyback transformers, and unidirectional drive circuits.
Advantages:
Balances large flux density plus low losses with regard to high-frequency applications.
five. 75-Series Cores
Important Features:
Lower core losses than Kool Mu and XFLUX cores.
Composed regarding microwave coil , aluminum, in addition to silicon for expense efficiency.
Applications:
Economical alternatives in low-loss applications.
Advantages:
Improved performance with value.
6. Amoflux Cores
Key Features:
Produced from amorphous ribbon powder with very soft saturation characteristics.
Programs:
PFC circuits, output chokes, computer servers, and industrial energy units.
Advantages:
Trusted and efficient underneath high-stress conditions.
Programs of Magnetic Powder Cores
Magnetic powdered cores are flexible and find make use of in numerous applications:
SMPS Output Filtration: Smoothen voltage output and improve energy efficiency.
Boost and even Buck Inductors: Aid in voltage step-up plus step-down conversions.
Flyback Transformers: Ensure effective energy storage in addition to transfer.
Power Component Correction (PFC): Boost power quality by minimizing reactive energy.
Energy Storage: Preserve energy flow found in critical systems this kind of as UPS.
Exactly why Choose Magnetic Powder Cores?
Efficiency: Their own ability to manage high frequencies and even reduce losses guarantees optimal performance.
Durability: Resistance to heat aging and low core losses assurance long-lasting operation.
Cost effectiveness: Options like Kool Mu and 75-Series cores offer high end at an inexpensive price.
Versatility: With materials suited to be able to various requirements, magnetic powder cores can easily be tailored to particular applications.
Bottom line
Permanent magnetic powder cores are indispensable in modern day power electronics credited to their productivity, stability, and elasticity. By selecting the proper core material for specific needs, industrial sectors can optimize their very own power systems plus achieve greater trustworthiness. Whether for SMPS, PFC circuits, or even energy storage, these cores ensure overall performance and cost-efficiency.